Are you involved in oil and gas projects? If so, this guide is for YOU to help prevent pollution during drilling and production, through processing and storage, to transmission and distribution. Many oil and gas companies are adopting Best Management Practices (BMPs) as an important part of their pollution prevention program to help them cut their air emissions, reduce water use, control erosion, and reduce the amount of hazardous waste that they generate.
Pollution Prevention (P2) is about reducing the amount of any hazardous substance, pollutant, or contaminant released into the environment in order to reduce the hazards to public health and the environment. Pollution Prevention is also about preserving resources through wise use.
The following BMPs will need to be judged on a case-by-case basis, taking into account the conditions, operations, and limitations of each facility. The best time to begin identifying BMPs is before a project begins. Many of the following BMPs can help you comply with regulations that are required by law.
DEQ’s Courtesy Leak Detection Program
DEQ is now offering courtesy leak detection audits, using infrared cameras (IR). Leak detection and repair programs are a cost-effective, proven emission reduction strategy for the oil and gas industry.
Top Ten BMPs for Construction Sites
1. Reduce Emissions During Drilling/Completions
- Use Reduced Emissions Completions (RECs), aka Green Completions, to capture gas produced during well completions that is otherwise vented or flared. Electricity needed.
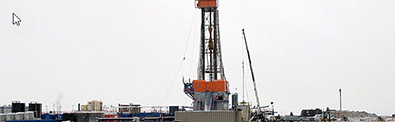
2. Reduce Emissions During Production
- Use enclosed tanks, central or on-site water treatment facilities instead of open pits to reduce fugitive air emissions.
- Minimize venting and/or use closed-loop process where possible during “blow downs.”
- Install a plunger lift system for removing liquids from wells or “blow downs.”
- Convert to low-emitting engines.
- Tighten connections and replace packing to minimize leaks and fugitive emissions.
- Use and maintain proper hatches, seals, and valves to minimize air emissions.
- Use vapor recovery units on oil, condensate, produced water storage tanks, and dehydrators.
- Reduce emissions of unburned hydrocarbons by routing emissions to flare or combustor or routing dehydrator still emissions to first stage compression.
- Lower glycol circulation rate to avoid over-dehydrating.
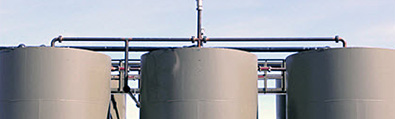
3. Conserve Water
- Utilize central water treatment facilities.
- Utilize on-site water treatment facilities, such as a 3-phase (liquids, condensate, and gas) separator on the flowback fluid to filter out heavy particulates so water can be reused. (See Case Study.)
- Use carefully planned well completions.
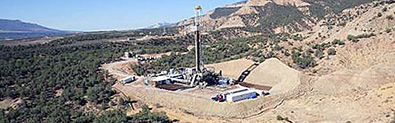
Case Study: Ultra Resources
Ultra Resources, based out of Houston, Texas, is creating solutions for a cleaner, smarter, and more secure energy future by utilizing an on-site flowback processing unit. The flowback treatment process is able to provide a reliable supply of 100% recycled water for subsequent operations. The process is very important in an area of high activity where water volume and water quality are necessary for successful operations.

Background
The flowback treatment process first utilizes a sand trap on the flowback fluid to capture heavy particulates (sand) so that the liquid phase can be sent to a 3-phase separator, where the liquids, condensate, and gas are segregated. The “water” is then sent through a series of 3 to 4 tear drop tanks that are used to settle out more particulates (light and heavy), while the condensate and gas are sent to a gathering facility. The tanks operate solely on a gravity/spillover feed. Flocculant and coagulant agents are added to the fluid stream ahead of the 1st tear drop tank to assist with the separation of particulates in the water. This on-site treatment system is capable of providing 2,000 bbls of recycled flowback water for reuse.
Environmental and Economic Benefits
- Save money through operational efficiencies. Water Hauling
- Water Processing
- Disposal
- Reuse flowback fluids; reducing the amount of water needed from another source.
- No Fresh Water Used Since 2007
- Eliminate the use of reserve pits which are sources of VOC emissions and potential leaks into surface or groundwater. Operations are closed loop; no pits.
- Water is piped to and from the operation.
- No flaring or venting.
4. Less Toxic Materials
- Substitute organic additives, polymers, or biodegradable additives for oil-based mud to reduce toxicity.
- Buy less volatile solvents and liquid chemicals in bulk and keep containers covered.
- Lubricate with mineral oil and lubra-beads instead of diesel oil.
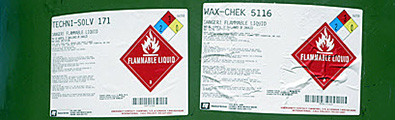
5. Reuse Materials
- Recover and reuse weighting materials and drilling fluids. Waste drilling mud can be reused at other locations for spudding or plugging and abandoning operations.
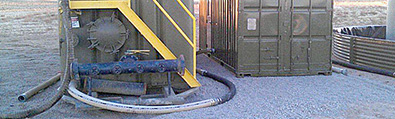
6. High-Efficiency Equipment
- Replace high bleed valves with compressed air, electric valves, or low bleed valves.
- Install or convert gas-operated pneumatic devices to electric, solar, or compressed air driven devices/controllers.
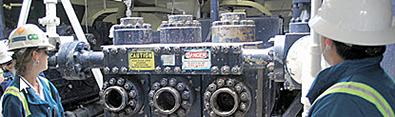
7. Monitoring and Maintenance
- Implement a Directed Inspection and Maintenance program to identify fugitive gas leaks from leaking compressors, valves, connectors, seals, and open-ended lines using infrared cameras, organic vapor analyzers, soap solutions, and ultrasonic leak detectors; and measurement devices, such as calibrated bagging, rotameters, and high volume sampler.
- Store drums and other material undercover, such as in a trailer, shed or covering with a tarp.
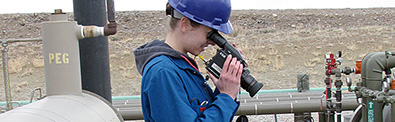
8. Dust and Tailpipe Emissions
- Apply water or chemical treatment, such as magnesium chloride, calcium chloride, lignin sulfonate, or asphalt emulsion.
- Restrict vehicle speeds to 10 mph on-site.
- Cover or reclaim excavated or inactive storage piles after activity ceases.
- Wash equipment and reclaim excavation faces.
- Use telemetry and well automation to remotely monitor and control production.
- Use centrally stored water that is piped to the well pads and fracturing facilities through a temporary surface line.
- Use centralized fracturing pads with hard-line frac pipes that can serve many well pads.
- Centralize (or consolidate) gas processing facilities (separation, dehydration, sweetening, etc.).
- Use vans and buses to shuttle employees to the worksite.
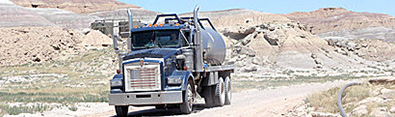
9. System Design
- Use directional drilling to drill multiple wells from a single pad, eliminating the need to construct separate well roads and pads.
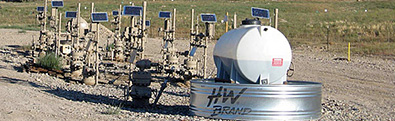
10. Construction and Reclamation
- Use diversion dikes, containment diking, and curbing to reduce exposure of stormwater runoff to cuttings and other waste storage areas.
- Segregate stormwater drainage from liquid storage, loading/unloading facilities and, operations areas from unimpacted areas.
- Use sediment traps, swales, and mulching during construction activities to reduce loss of sediment and contamination of runoff.
- Accelerate reclamation of the site.
- Reclaim disturbances.
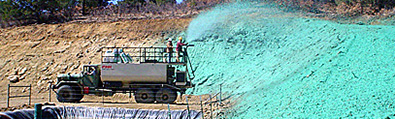
More Information
BLM’s Best Management Practices
The BLM’s Website provides information on BMPs that help ensure that energy development is conducted in an environmentally responsible manner.
EPA’s Natural Gas STAR Program
The Natural Gas STAR Program is a flexible, voluntary partnership that encourages oil and natural gas companies—both domestically and abroad—to adopt cost-effective technologies and practices that improve operational efficiency and reduce air emissions.